在“碳中和”和可持续发展的大方向上,汽车轻量化概念,作为实现汽车节能减排的重要路径,已得到社会、政府以及全球各大汽车制造商的广泛接受和认可。
(1)汽车轻量化是行业发展的重要方向
汽车轻量化,就是在保证汽车的强度和安全性能的前提下,尽可能地降低汽车的整备质量,从而提高汽车的动力性能,减少燃料消耗,降低排气污染。
根据美国铝业协会(The Aluminum Association)下属的铝业交通组(AluminumTransportation Group)的数据显示,汽油乘用车减重 10%可以减少 3.3%的油耗;柴油车减重 10%则可以减少 3.9%的油耗,而对于新能源电动汽车,轻量化带来的节能效果更为显著,减重 10%和 15%分别可以使电能消耗减少 6.3%和 9.5%。
汽车轻量化并不是简单地追求汽车的减重,还必须能够同时兼顾质量、性能和价格。基于铝合金材料易成型、轻质以及高回收率的特性,从汽车的制造、运营以及废旧汽车回收各个维度考虑,汽车铝合金压铸件在汽车上的应用都能带来巨大的经济效益,汽车铝合金精密压铸件以质量轻、性价比高的优势已经在汽车零部件行业占据了重要地位。
铝合金精密压铸件在汽车上应用的发展潜力受单辆汽车用铝量上升的刺激而得以挖掘。以在北美地区为例,平均每辆汽车的用铝量从 1975 年的 84 磅(约合 38.1kg)增长至 2020 年的 459 磅(约合 180.1kg),并预计 2030 年,北美平均每辆轻型车的用铝量将会达到 570 磅(约合 258.5kg)。
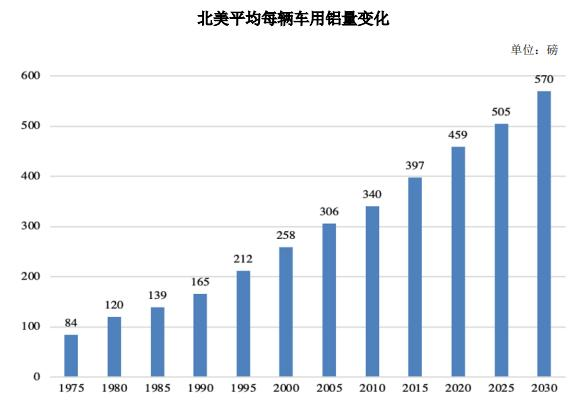
资料来源:DuckerFrontier
(2)新能源汽车产销量增长及渗透率提升,带动铝轻量化行业增长
新能源汽车产业链经过多年的成长发展,各个环节逐步成熟,丰富和多元化的新能源汽车产品不断满足市场需求,使用环境也在逐步优化和改进。在这些措施之下,新能源汽车越来越受到消费者的认可,产销量继续创新高。
根据中国汽车工业协会数据显示,我国新能源汽车 2021 和 2022 年度产量分别为 354.5 万辆和 705.8 万辆,销量分别为 352.1 万辆和 688.7 万辆,2022 年度新能源汽车的市场占有率已提升至25.6%,中国新能源汽车市场已经进入政策驱动及需求驱动并行的高增长期。
根据国际能源总署(IEA)及 Marklines 数据统计,2021 年和 2022 年美国新能源汽车销量分别为 63.0 万辆和 98.5 万辆,销售增长率分别达 114.29%和 56.29%,渗透率于 2022 年度首次突破 5%。
新能源汽车催生铝合金压铸新赛道。新能源汽车虽然取消了发动机系统,但其电池包、电驱动系统等壳体仍采用铝合金压铸材质,且因需集成冷却系统,制造工艺上更加复杂。与燃油车相比,电动车在车身、底盘结构件上更加积极采用铝合金压铸件。随着高真空压铸工艺、大吨位压铸机的发展,铝合金压铸的结构件可以满足性能上的要求,使得该类产品在新能源车得以普及。
平均单车用铝量方面,以北美市场为例,2020 年纯电车型为 643 磅(约合291.7kg),非纯电车型为 454 磅(约合 205.9kg),纯电动汽车较内燃机汽车高出 40%,在新能源渗透率整体尚不够高的情况下,所有车型的平均单车用铝量为459 磅(约合 208.2kg),据预测,2026 年北美市场整体的平均单车用铝量将达到 514 磅(约合 233.1kg)。
(3)电动化催生一体化压铸等新赛道,一体压铸是未来行业发展大趋势
纯电动汽车不同于传统燃油车,电池+电机取代发动机成为汽车的动力输出系统。电驱动系统设计经历了独立式、二合一、三合一和多合一的发展阶段。电驱系统集成更多功能是大势所趋,电驱动壳体的设计也将从独立式走向集成式设计:从分体式简单集成,即减速器、电机和电控有各自独立的壳体设计,到电机、减速器壳体一体化和三大件壳体一体化。
随着更多功能集成到电驱动中,壳体也将叠加更多的功能设计。电机、电控及减速器都需要冷却系统,壳体的设计需要考虑冷却管路的设计和布局。这对壳体供应商的产品开发和设计能力提出了较高的要求。
一体化压铸是汽车结构简化的大趋势。一体化压铸车身是轻量化技术的升级,减少车身零件数量,使得车身结构大幅简化;在轻量化的同时,简化供应链环节,具备降低车重减少电池成本、原材料利用率高、工厂占地面积减少等多种优点,实现汽车组装效率大幅提升。
随着汽车轻量化、一体化和大型化发展,品成金属自2021年起积极布局国内市场,引进技术人才和先进设备,将模具生产能力提升至6600T,不断新增新能源模具订单,已为国内多家头部客户生产新能源压铸模具。
欢迎致电品成金属进行技术交流及项目开发合作!
文字来源:思瀚产业研究院